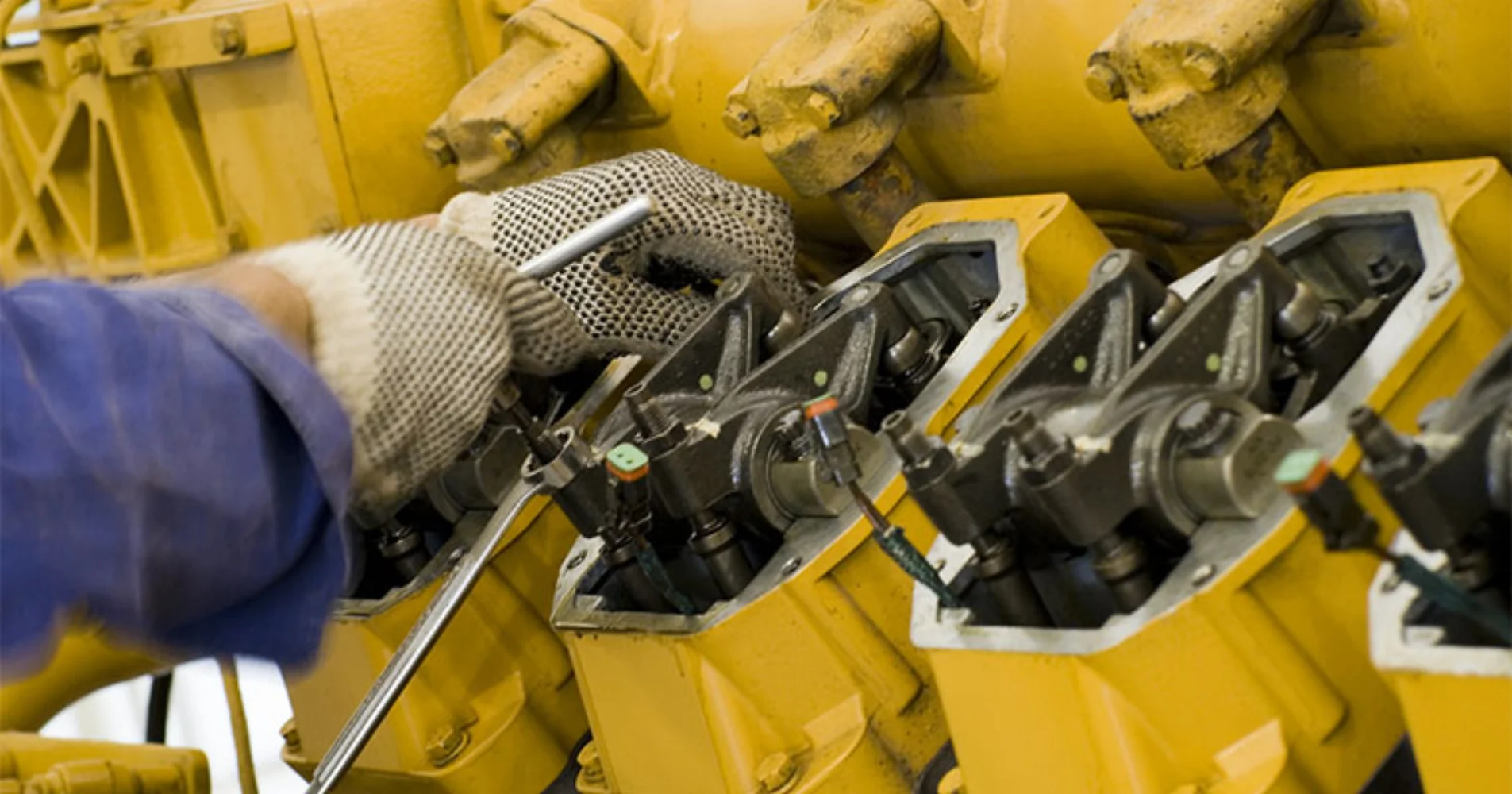
Generator Maintenance Checklist
Server Room Environments supplies and supports a wide range of generator and UPS installations protecting server rooms and datacentres.
Our project managers operate a nationwide generator service and maintenance team and provide a 24/7 emergency call out service, generator maintenance contracts and planned preventative maintenance visits.
Preventative maintenance visit schedules can be tailored to suit individual sites and generating sets. This is the general checklist our generator engineers work to.
item | Task | 3 Months | 6 Months | 12 Months |
---|---|---|---|---|
1 | Upon arrival the Engineer will report to the site representative to explain purpose of visit | yes | yes | yes |
2 | Safety / Site induction to be carried out as required | yes | yes | yes |
3 | Visual inspection of equipment & surrounding area required, Equipment & work area to be checked for safe operation & free from slip / trip hazards etc | yes | yes | yes |
4 | PPE to be worn | yes | yes | yes |
5 | Ensure Proper warning notices are in place | yes | yes | yes |
6 | Check that all Electrical panels / terminations are properly secured | yes | yes | yes |
7 | Check integrity of earthing system | yes | yes | yes |
8 | Generator run-up off load for 10mins | yes | yes | yes |
9 | Generator checks carried out for leaks, excessive noise, vibration & exhaust emissions – Customer to be notified of any major issues at this time | yes | yes | yes |
10 | Generator outputs to be recorded – Voltage, Frequency, oil pressures etc | yes | yes | yes |
11 | Check that all guards are in place around moving parts | yes | yes | yes |
12 | Check Engine Lubricant oil levels – top up as required | yes | yes | yes |
13 | Replace Oil filters & Engine lubricant oil | – | – | yes |
14 | Check Fuel filters – Drain sediment traps | yes | yes | yes |
15 | Replace Fuel Filters | – | – | yes |
16 | Check Coolant levels – top up as required (anti-freeze mixture 50/50) | yes | yes | yes |
17 | Replace Coolant filters if applicable | – | – | yes |
18 | Check air filters – Clean if necessary | yes | yes | yes |
19 | Replace air Filters (annually or Bi-annually subject to condition / type) | – | – | yes |
20 | Check radiator condition – Clean as required (Authorisation required if pressure washing required | yes | yes | yes |
21 | Check Turbo for correction operation | yes | yes | yes |
22 | Check Engine/crankcase Breather for excessive emissions | yes | yes | yes |
23 | Inspect all hoses for condition | yes | yes | yes |
24 | Check all fixings, retaining bolts and Anti-Vibration mountings | yes | yes | yes |
25 | Visual Inspection of main Alternator – condition/couplings/bolts etc | yes | yes | yes |
26 | Check Fuel lines, change-over valves, couplings, transfer pumps, switches | yes | yes | yes |
27 | Check Governor operation, Drain/refill lubricant if applicable | yes | yes | yes |
28 | Clean & lubricate all linkages | yes | yes | yes |
29 | Check Fire valve condition / integrity | yes | yes | yes |
30 | Inspect Gauges for operation / condition | yes | yes | yes |
31 | Check & Adjust valve clearances | – | – | yes |
32 | Check Jacket water heater operation | yes | yes | yes |
33 | Check Water pump – Pulley bearing for wear, grease if applicable | yes | yes | yes |
34 | Check Battery condition – Terminals / cables / Electrolyte level | yes | yes | yes |
35 | Test battery under load where possible | yes | yes | yes |
36 | Check Charging system – Fan belt condition/adjust as required, Pulley bearing for wear, Alternator output | yes | yes | yes |
37 | Check Battery mains charger operation | yes | yes | yes |
38 | Check starter motor operation | yes | yes | yes |
39 | Check control panel / meters & interrogate fault/history logs if available | yes | yes | yes |
40 | Check shut-down devices (oil pressure/over-speed/coolant etc) | yes | yes | yes |
41 | Inspect Wiring loom for signs of damage / wear | yes | yes | yes |
42 | Visual check on all switches / fuses | yes | yes | yes |
43 | Check electrical meters | yes | yes | yes |
44 | Visual inspection of Change-over contacts if applicable | yes | yes | yes |
45 | Check Control panel / switches / fuses / relays | yes | yes | yes |
46 | Visual inspection of circuit breakers | yes | yes | yes |
47 | Visual inspection of Synchronisation equipment if fitted, Reverse Power relay, Synch checks, etc | yes | yes | yes |
48 | Check Termination boxes – clean as required | yes | yes | yes |
49 | Check Engine heater | yes | yes | yes |
50 | Inspect Alternator covers – Clean as required | yes | yes | yes |
51 | Check Engine AVR/DVR, droop controls, etc | – | – | yes |
52 | Adjust Voltage / Frequency – Customer authorisation required | yes | yes | yes |
Fuel Services and Condition Monitoring
Our generator team also provide fuel supply and condition monitoring services. The team can provide an oil and fuel analysis. Using a sampling kit our engineers can provide certified results within a few days and a report showing any contaminant levels with interpretation of the results.
The analysis looks for the presence of several metals, fuel and water including: Copper, Iron, Chromium, Aluminium, Lead, Tin, Carbon, Sodium, Fuel and Water. This can help to identify coolant leaks, excessive cylinder lining wear, piston ring wear, bearing wear, fuel ingress and air filtration problems.
Load Bank Testing
As part of a generator commissioning or planned preventative maintenance visit our generator team can provide load bank testing from a fleet of mobile load banks.
Thermal Imaging
‘Hot spot’ analysis via thermal imaging is a service we use within server room and datacentre environments and external installations. Thermal imaging of the generator, UPS system and electrical circuitry, LV switchboards and panel distribution can identify overloads and the potential for electrical circuit breakdown.
To arrange a generator installation, maintenance inspection, load bank testing or thermal imaging survey please contact the projects team at Server Room Environments.